A Hands-On Journey as a Maintenance Engineer Intern at AJ Total Group

During my internship at AJ Total Group, one of Korea’s leading temperature-controlled logistics companies, I had the incredible opportunity to work at their state-of-the-art facility in Long Hau Industrial Park, Long An. Spanning 25,600 square meters, the facility houses five forklift-operated warehouses and a massive automated warehouse accommodating up to 30,000 pallets. As an intern, I worked alongside two senior engineers, gaining invaluable hands-on experience in troubleshooting, maintenance, and system optimization.
Troubleshooting & System Maintenance
From my first day, I was immersed in the fast-paced environment of warehouse operations. My primary role involved assisting senior engineers in troubleshooting mechanical and electrical issues across various automated systems. Whether it was a forklift experiencing electrical malfunctions or a robotic arm misaligning pallets, I was actively involved in diagnosing and resolving problems. One of my most memorable experiences was working on a temperature control system malfunction, a critical issue in a facility where precise conditions are essential for preserving perishable goods. Under the guidance of my mentors, I learned to analyze sensor data, recalibrate temperature settings, and restore system efficiency.
Data Analysis & Preventive Maintenance
Beyond hands-on repairs, I also played a key role in maintaining maintenance records and analyzing equipment performance. I helped track downtime patterns and identify recurring issues, which led to proactive solutions rather than reactive fixes. In one instance, after reviewing system logs, I noticed a particular conveyor belt had required frequent maintenance over the past two months. I suggested an adjustment in its lubrication schedule, which significantly reduced future breakdowns.
Additionally, I assisted in implementing efficiency improvements to enhance reliability. By working closely with senior engineers, I gained exposure to predictive maintenance strategies, where we used historical data to anticipate failures before they occurred. This approach not only improved system reliability but also reduced operational disruptions.
Working with Automated Robotic Systems
One of the highlights of my internship was inspecting and repairing the automated robotic systems that streamlined warehouse operations. These robots were responsible for transporting, stacking, and organizing thousands of pallets daily, ensuring seamless logistics efficiency. I was entrusted with conducting routine system diagnostics, checking for misalignment, and making minor adjustments to robotic sensors and motor functions.
A particularly rewarding experience was troubleshooting a robotic malfunction where a misconfigured sensor caused repeated placement errors. After carefully inspecting the system and analyzing performance data, I assisted in recalibrating the sensor and updating the software settings. Seeing the robot resume flawless operation was an incredibly satisfying moment, reinforcing the importance of precision and problem-solving in maintenance engineering.
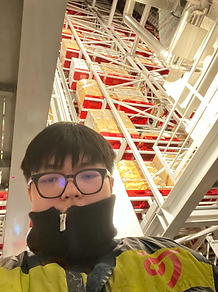
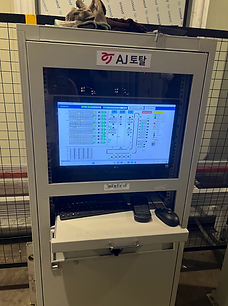





Reflections & Takeaways
Throughout my time at AJ Total Group, I developed a strong technical foundation in mechanical and electrical maintenance, data-driven troubleshooting, and robotic system optimization. Working in a high-tech, temperature-controlled logistics environment challenged me to think critically, adapt quickly, and embrace teamwork.
This internship solidified my passion for engineering and automation, giving me firsthand experience in improving operational efficiency and ensuring system reliability. More importantly, it taught me the value of proactive problem-solving, a skill I am eager to carry forward in my future career.